Industry 4.0: Strategic Approaches to Maximize Growth and Efficiency
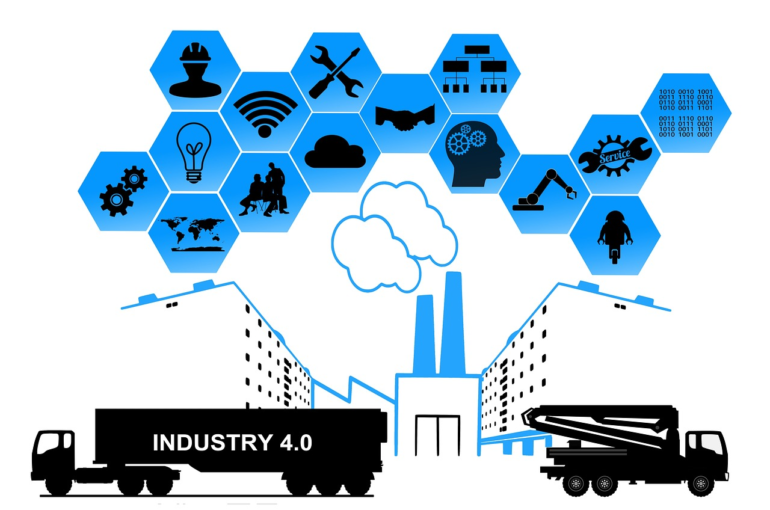
Welcome to this comprehensive blog, where we will talk about the exciting transformation happening in the manufacturing industry – Industry 4.0. This revolutionary concept blends digital technologies with traditional production processes, ushering in the Fourth Industrial Revolution. With the convergence of leading-edge technologies like the Internet of Things (IoT), Artificial Intelligence (AI), Big Data Analytics, and Cyber-Physical Systems (CPS), Industry 4.0 creates an intelligent and interconnected ecosystem.
Furthermore, We’ll take you through the essential steps to successfully implement Industry 4.0 in your business. By doing so, you can know many benefits, including improved efficiency, significant cost savings, and an unparalleled level of innovation. So, let’s explore this exciting journey into the future of manufacturing!
Step 1: Incorporate the power of Industry 4.0 Advancements
Industry 4.0 opens up a world of possibilities by seamlessly integrating advanced technologies into the manufacturing landscape:
Internet of Things (IoT)
Imagine connecting everyday objects and machines to the internet, allowing them to communicate with each other. In the manufacturing realm, we deploy IoT devices and sensors on the shop floor and equipment, gathering real-time data on performance, temperature, pressure, and more. This data-driven approach not only empowers us to make smarter decisions but also helps us to optimize processes proactively.
Artificial Intelligence and Machine Learning (AI/ML)
With AI and ML on board, machines gain cognitive abilities to analyze massive amounts of data, recognize patterns, and even make autonomous decisions. That means we can automate repetitive tasks, forecast demand, and predict potential equipment failures. As a result, boosted productivity and less downtime.
Big Data Analytics
In the era of Industry 4.0, data takes center stage. Big Data Analytics processes and analyzes large datasets to uncover valuable insights, patterns, and trends. Armed with this knowledge, we can identify inefficiencies, fine-tune production schedules, and stay ahead in a dynamic market.
Cyber-Physical Systems (CPS)
CPS brings the physical and digital worlds together by connecting machines and systems through networks. Additionally, this creates a harmonious cyber-physical synergy where data from physical assets informs real-time decision-making and action. By streamlining operations and responding nimbly to market demands, we can achieve operational excellence.
Step 2: Assess Your Readiness and Bridge the Gaps
Before gearing up for the exciting Industry 4.0 journey, it’s essential for manufacturers to evaluate their current state and identify areas for improvement :
Uncover Challenges
Take a close look at your organization to identify existing pain points and challenges. Whether it’s inefficiencies, production bottlenecks, quality control issues, or high maintenance costs, understanding these hurdles is the first step towards overcoming them.
Optimize Data Collection
The backbone of Industry 4.0 lies in data, so it’s crucial to evaluate your data collection methods. Ensure that they provide the relevant and accurate information needed for seamless implementation. Subsequently, you might need to invest in additional sensors or upgrade your data storage and processing capabilities to keep up with the demands of this digital era.
Empower Your Workforce
Industry 4.0 requires a digitally savvy workforce. Firstly, Assess the skill levels of your employees and identify any gaps that need to be filled. Offering appropriate training will equip them with the expertise to operate and leverage digital technologies effectively.
Step 3: Craft a Winning Implementation Strategy
To get into Industry 4.0 successfully, a well-defined implementation strategy is key:
Nail Your Goals
It all starts with setting clear and achievable goals that align with your overall business objectives. Whether it’s ramping up production efficiency, reducing downtime, optimizing resources, or improving product quality, defining your targets is crucial.
Choose Smart Technologies
With a vast array of Industry 4.0 technologies out there, it’s essential to pick the right ones tailored to your unique needs and long-term vision. Furthermore, teaming up with reliable technology vendors can simplify this selection process.
Time it Right
Remember, Rome wasn’t built in a day, and neither is your Industry 4.0 transformation. Create a realistic timeline that accounts for the complexities of integrating new technologies while minimizing disruptions to your existing operations.
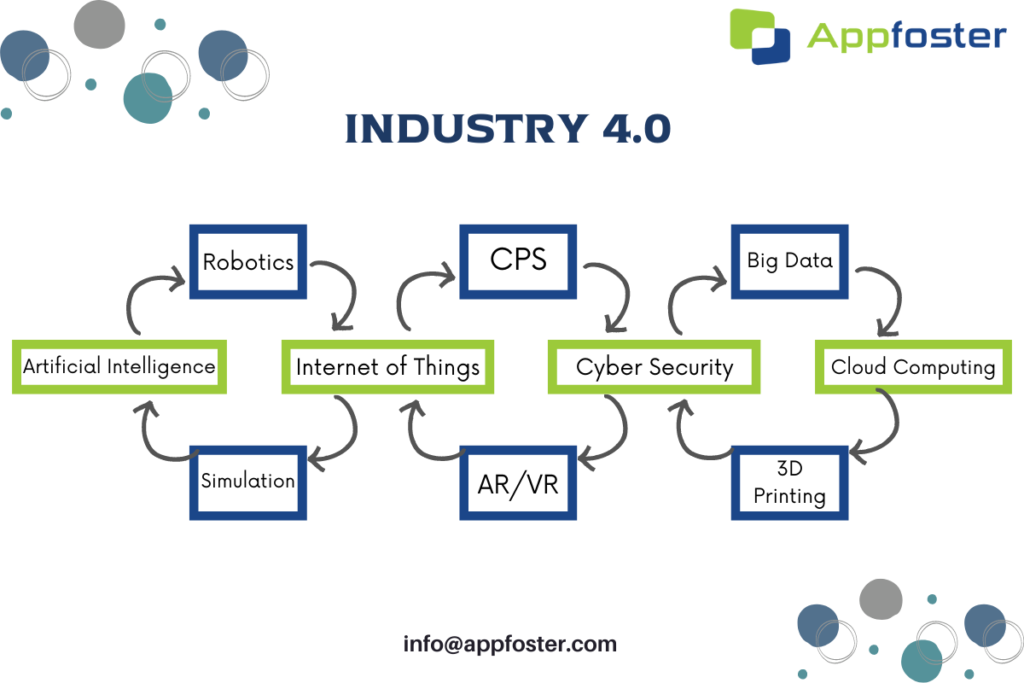
Step 4: IoT and Streamlined Data Management
In the Industry 4.0 era, integrating IoT devices and optimizing data management are vital components:
Go Smart with IoT
By installing IoT sensors on production equipment, manufacturers gain real-time insights into their performance. This not only empowers them to predict maintenance needs but also proactively address potential breakdowns, resulting in reduced downtime and prolonged equipment lifespan.
Lock Down Data Security
With increased device connectivity and data sharing, robust cybersecurity measures are surely paramount. Manufacturers should implement secure data encryption, and access controls, and conduct regular security audits in order to protect sensitive information from cyber threats.
Take in the Cloud
Cloud-based platforms offer scalable and certainly cost-effective solutions for data storage, processing, and accessibility. Thus, by adopting the cloud, seamless data sharing across departments and manufacturing sites becomes a reality, enhancing collaboration and informed decision-making.
Step 5: Captivating AI and Machine Learning Abilities
AI and ML technologies have an outstanding impact on overall processes:
Stay One Step Ahead with Predictive Maintenance
Thanks to AI-driven predictive maintenance, manufacturers can especially foresee equipment failures by analyzing historical data patterns. Ultimately, this proactive approach reduces downtime, cuts maintenance costs, and boosts overall equipment effectiveness (OEE).
Supercharge Quality Control with AI
Imagine real-time defect detection during production using AI-powered image recognition systems. By automating quality control, manufacturers can minimize product defects, waste, and the need for manual inspections.
Boost Efficiency with AI-Driven Optimization
Tap into the potential of AI algorithms, analyzing vast datasets to optimize overall production schedules, resource allocation, and workflow. It results in Improved efficiency, reduced lead times, and finally more reliable manufacturing process.
Step 6: Smart Decision-Making with Big Data Analytics
Leveraging big data analytics is a game-changer for data-driven decisions:
Visualize Data for Quick Insights
Interactive dashboards and reports offer real-time information on key performance indicators (KPIs). Manufacturers can keep an eye on production metrics, spot trends, and make informed decisions without delay.
Fine-Tune Processes with Historical Analysis
Dive into historical data to identify inefficiencies and production bottlenecks. By continuously refining processes, manufacturers can ramp up productivity and resource utilization.
Predict Demand Like a Pro
Advanced analytics can predict demand patterns, enabling manufacturers to optimize inventory levels and adjust production output accordingly. Accurate demand forecasting means better market responsiveness and cost savings.
Step 7: Empowering Your Workforce with Digital Skills
In the ever-evolving Industry 4.0 landscape, your workforce holds the key to success:
Encourage Training Initiatives
To keep your manufacturing team at the forefront, further, invest in robust training programs. These initiatives generally equip employees with digital prowess, data analysis skills, and cybersecurity know-how. Empowering your workforce to navigate new technologies confidently ensures smooth adaptation to the changing manufacturing landscape.
Cultivate a Culture of Innovation
Nurture a culture where continuous learning and innovation thrive. Encouraging this mindset empowers your employees to embrace change and actively contribute to process optimization and product development. By fostering creativity and adaptability, you create a dynamic and future-ready workforce.
Closure
In conclusion, Industry 4.0 represents a seismic shift in the manufacturing realm, ushering in a new era of growth and efficiency. With the integration of cutting-edge digital technologies, streamlined data management, and a digitally empowered workforce, manufacturers can unlock a world of untapped potential, driving unparalleled productivity, cost savings, and competitive advantages. This isn’t just a fleeting trend; it’s a transformative journey that will reshape the future of manufacturing, leading us into a smarter, interconnected era of industrial production.
Appfoster provides comprehensive digital transformation solutions for manufacturers, helping to be up to date with the Industry 4.0 revolution. With expertise in AI, Big Data, and more, We empower you to adopt advanced technologies and optimize processes. We enable you to stay competitive in a rapidly evolving global market.